 |
Acid Recovery & Concentration Plants |
A) Sulphuric Acid Concentration Plant (SAC):-
Sulphuric acid is used in many processes in chemical plants, thus making spent acid quite diluted. Disposing of this spent acid becomes an environmental pollution problem besides a waste of precious resource. The diluted spent acid can be efficiently re-concentrated upto a maximum concentration of 96% (w/w) and reused in the main plant process, thus saving the environment and that too by improving the economical bottom line. Thus sulphuric acid recovery or concentration plant is a fantastic option for high sulphuric acid users in process plants.
Concentration of Sulphuric acid is mostly performed under vacuum in order to reduce the operating temperature, especially for high concentrations. We offer turnkey solutions right from know-how & technology, to supply, installation &commissioning. Our plant comprises of equipments wherin the wetted parts are made up of Borosilicate glass 3.3, Fluoropolymers (PTFE, PFA, FEP, PVDF, PP, etc), High Nickel alloys, Graphite & exotic metals (Ta, Ti, Nb, etc.).
The plants can be totally automated by PLC or DCS based systems and even integrated with computers (SCADA etc).
B) Nitric Acid Concentration:-
Concentrated Nitric Acid CNA ( i.e. high-strength nitric acid at 98 -99% w/w.) is an important chemical for Chemical & Pharmaceutical industries in general (like polymers & plastics, dyestuff, bulk drugs, explosives, Fertilizers and other important organic nitro-compounds). This acid is frequently used as "nitrating acid".
Industrially manufactured Nitric acid is obtained as a weak acid solution, at a concentration of about 65% -67% w/w (max.), which is of no use whatsoever for the various processes stated above. Owing to the physical behaviour of the nitric acid / water system, it is not possible to remove excess water from this weak acid by a fractional distillation process because this solution forms an azeotrope, a constant acid / water boiling composition at about 68% w/w. acid.
To concentrate this acid further an extractive distillation process by adding concentrated sulphuric acid needs to be employed. While the water goes this sulphuric acid gets diluted, which can be again re-concentrated and reused for the concentration of dilute nitric acid again.
Reconcentration of weak Sulphuric Acid:-
The dilute sulphuric acid stream coming off the bottom of the Extractive Distillation Column is reconcentrated back to the same service by using BVR's sulphuric acid re-concentration plant, which can be coupled directly with the nitric acid concentration system so that no cooling of the weak sulphuric acid is necessary, thus saving a large amount of heating energy for the economical benefit of the user.
NOx Absorption:-
The NOx gases escaping from the Nitric acid Concentration System, along with bleaching air, are absored in BVR's special NOx absorption plant and is recycled back into the main system as an aqueous solution of nitric acid, at concentration comparable to those of the nrtric acid feed to the same System : the residual gases vented to the atmosphere have NOx. content below the acceptable values as per environmental norms.
Pre-concentration of weak Nitric Acid solution:-
Whenever a solution of Nitric Acid is too weak for direct Extractive Distillation (typically below 45% -50% w/w.), it can be pre-concentrated to its azeotropic grade by ourvacuum Fractional Distillation plant.
C) HCl Concentration & Recovery:-
The material system hydrogen chloride/water displays a maximum azeotrope at a boiling temperature of 108.6°C, for a system pressure of 1 bar and a HCl concentration of 20.2wt%. If the acid concentration is lower than the azeotrope mixture, the acid can be concentrated only up to the azeotropic point. Further concentration needs special procedures. We have considered the most economical contemporary technology “Extractive Rectification & Absorption Technology”.

Extractive Rectification & Absorption Technology:-
As mentioned this is an economical technology the azeotrope point is suppressed as best as possible and increases the relative volatility of HCl. The relative volatility may be impacted by change of the activity coefficients. This is achieved by addition of a third ingredient, the extractive agent, which displays strong hygroscopic properties. Conc. HCL & HCl gas is produced at the head of the extractive rectification column upon choice of an appropriate extraction agent. In the column the extraction agent is diluted with water, which is extracted in a selective fashion from the inflowing mixture. Subsequently, the extractive agent is recycled and newly fed into the extractive rectification process.
Sulphuric acid, and aqueous solutions of CaCl2 are appropriate extraction agents for the concentration of hydrochloric acid.
|
 |
Solvent Recovery Plants |
|
|
Recovery of Solvents from process wastes:- |
|
Solvent Recovery Like Acetone, Toluene, IPA, Ethanol, Methylene Chloride and many other inorganic and organic solvents.
Processes employed are Distillation (including azeotropic distillation), Extraction (Liquid-liquid & solid-liquid), Absorption, etc.
We take up studies for the best possibilities of recovering solvents and other important chemicals from the liquid discharges as well as gaseous exhausts.

Bromine Recovery
Bromine can be recovered from two sources :
1) From Sea Bitterns
2) From Industrial effluents
BVR offers turnkey projects for the recovery of Bromine from both the aforesaid sources.
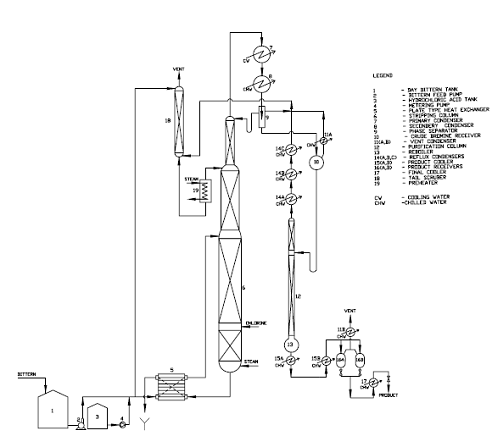
Two processes are generally adopted for the recovery of Bromine from Sea/ Salt Bittern as mentioned below:
a) Steaming Out Process (Hot Process) :
The process is also known as “Hot Process” because chlorination of bittern is done with simultaneous steam blowing by means of live steam to heat the bittern to near its boiling point to set free the finished product Bromine.
b) Air Blowing Process (Cold Process) :
This process is known as “Cold Process” because the finished product Bromine is set free from bittern by chlorination and air blowing under cold conditions.
Absorption of Industrial exhaust gases like SO2, SOx, NOx, Chlorine Cl2, HBr etc.
We offer turnkey solutions for absorption of exhaust gases after carrying out detail onsite studies. Our focus is to satisfy the environmental pollution requirement and also try to recover the exhaust gases in such forms so that they can be reused for various processes thus adding to the bottom line.

Both Adiabatic absorption and Isothermal Absorption processes are employed in order to get the most efficient output.
Please contact us for further discussions if you need us to study your plant.
Volatile Organic Compounds (VOC) Removal from Gaseous / Air / Liquid / Water streams
The removal of VOC from gaseous streams, before they can be vented, and from the liquid / water streams before they can be released are Pollution Control measures. Environmental pollution control has now become more stringent as industries, world wide need to comply with these issues responsibly.
The removal of VOC requires competent technology and engineering capabilities, in order to obtain these compounds either for re-use or to release them off to the environment within the acceptable limits.
We at BVR work out tailor-made solutions for our clients by studying their discharges (gaseous / liquid). Various unit operations are employed by the use of right technology & engineered systems. In the process many a times besides controlling the discharge composition within the environmental limits, recover a lot of re-usable components that adds to the bottom line of their commercial realisation.
 |
|
HCl Gas Absorption |
HCl gas can be economically absorbed forming Hydrochloric acid of 30% (w/w) concentration which can be re-used in the main process. Thus this absorption is a pollution abatement as well as a recovery process.
The absorption can be done by two different methods :
1) Adiabatic Absorption: This method is suitable when the inerts like air, phenolic compounds etc are substantial.
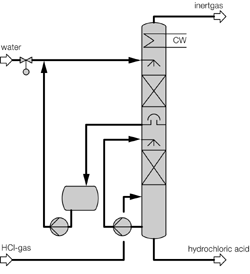
2) Isothermal Absorption: This method is suitable when inerts like air phenolic compounds, etc ar negligible.
Please contact us for your exact requirement.
|
Sulphuric Acid Dilution |
Sulphuric acid is a heavy chemical and finds numerous applications in the industry. It is the product of ‘Contact Process’ and commercially availabl as 98.5% (w/w) H2SO4 or stronger in the form of oleum.
However, many of the processes and applications utilizing sulphuric acid require weaker acid than this. As a result, dilution equipment is often necessary in order to meet the requirement for this weaker acid.
During dilution considerable heat is generated depending on the extent of dilution desired. The Integral heat of solution of sulphuric acid is plotted in fig.1. The heat liberated sometimes is sufficient to produce boiling of the acid and so, provision is made for the re-circulation of a portion of cooled dilute acid, thus ensuring working at controlled temperature.
From the above it will be clear that intimate mixing and efficient heat transfer form the pre-requisites for sulphuric acid dilution unit to avoid excessive temperature and local heating and uniform product concentration.
Process Description:
Metered quantity of sulphuric acid is introduced to a heat exchanger with re-circulation of water through a pump from the tank containing pre-determinant quantity of water. The turbulence created in the heat exchanger ensures both intimate mixing and efficient heat transfer. When desired strength of acid is reached, the contents of the tank is transferred to storage and fresh batch can be started again.
System Benefits:
1. High product quality is guaranteed as glass is completely inert to sulphuric acid.
2. Available in wide range of concentrations and capacities.
3. Simple and easy to operate.
4. Operational reliability due to maintenance free in working.
5. Corrosion Resistant |
 |
These can be done by three different routes :
a) Sulphuric Acid Route Up to 200 Kg/Hr. Spent Acid (70% H2SO4) as by product.
b) Azeotropic Boiling Route Up to 200Kg/Hour. Spent Acid (20% HCl) as byproduct .
3) Extraction or CaCl2 Route
General Features:
- Turn-down ratio of 25%
- Continuous operation.
- Practically maintenance free operation.
- Low cost of production.
- Intrinsic safety tool.
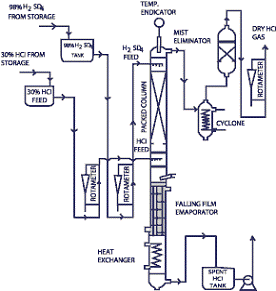
Process Design & Engineering for Distillation, Extraction, Absorption, Reaction, Separation, and other unit operations from Lab to Production scale. |
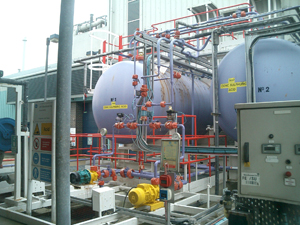
P&ID Development
Process Modelling
Heat Exchanger Design
Equipment Specifications & Datasheets preparation
Heat & Material Balance
Pump Design
Piping Design
Process Optimisation
Process Validation & documentation (3Q / 4Q)
Experience in dealing with equipment requirements, automation at lab or plant level, Onsite installation, commissioning and training Specifications Investigation and analysis / calculations : pumps, valves, flow meters, temperature/pressure measuring devices.
Preparation of documents / manuals / qualification for clients as per protocols and 3Q/4Q.
We use variety of software to simulate processes, setup and configuration of
modelling and control software.
Detailed process design PFD, BFD, Mass Balance, preparation of Equipment datasheets, Basis of Safety study – for new product launch- scaling up from Lab to Pilot scale before final production.
Heat, Mass balance, HYSYS Simulation, Vessel/Separator, Columns, Pumps, Heat Exchanger sizing & design.
Project Management, Process Design, Commissioning, Equipment Maintenance, Process Monitoring, Testing, Validation (as per the standard procedures), Plant Data Monitoring, Process Software Troubleshooting, Maintenance Life Plans, HAZOP, Basis of Safety study , SIL etc. , Awareness of H&S regulations, CDM Regulations, API, BS-EN, European Directive Standards, Awareness - HAZOP
Equipment Condition Survey, Capex Plan Estimates |
|
|
|
|
For
Further Inquiry Pl. Contact at |
 |
|
Alternate Website : www.bvres.com |
D115,
Lakulesh Avenue,
Delux Charasta, Nizampura,
Vadodara - 390002,
Gujarat, INDIA.
Ph. No.-- : +91 265 3254050
Fax No.-- :+ 91 265 2784268
Mob. No. : +91-9824037528, 9824099211,
E-mail---- : consult@bvrin.com |
|
----------------sales@bvrin.com |
|
|
|
Copyright
© BVR India.
All Rights Reserved.
|
|
|