ENGINEERED UNITS
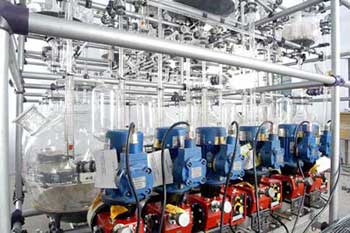
These are specially fabricated & assembled units made up of a combination of Borosilicate 3.3 Glass as per ISO 3585, PTFE, PTFE-lined & Exotic Metals ; designed , fabricated & engineered as per ENBS 1595, AD2000 Merkblatt, GMP, ASME Section VIII Div.1 & TEMA. And are available with - CE Mark ; designed & made in compliance with the relevant directives namely ; PED-97/23/EC, Machine Directive-98/37/EC, LVD-73/23/EEC, EMC Directive-89/336/EEC.
- Equipment Qualification / Validation with 3Q / 4Q documentation as per GMP norms.
- Assemblies for Piloting, Production, Pollution control, R&D
- A range of designs available & in modular construction
- Units for Heat transfer, Distillation, Reaction, Absorption, Evaporation, Crystallization, Extraction, etc.
- Miniplants, Pilot plants, Kilolabs, Bioreactors, Teaching units
- Units available for hazardous areas with flame-proofing
- Special custom designed assemblies can be made as per requirement
Corrosion Resistant Heat Exchangers
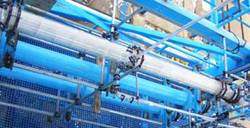
Shell & Coil type Heat Exchangers Immersion Heat Exchangers
Shell & Tube Heat Exchangers Bayonet type Heat Exchangers
U-Tube Tubular Heat Exchangers
- Material of construction comprise of combinations of highly corrosion resistant materials including Borosilicate 3.3 Glass , Fluoropolymers & Exotic metals (Ta, Nb, Ti, Hastelloy, etc.)
- Optimum Solution for every requirement with a range of designs available & in modular construction
- Wide range of duties namely ; Condensation, Cooling, Heating, Boiling & Evaporation
- Optimum Solution for every requirement with a range of designs available & in modular construction
- Wide range of duties namely ; Condensation, Cooling, Heating, Boiling & Evaporation
- Fabricated with all major internationally prevalent buttress design and having a very high reliability of the strong and high-duty coupling system used for all components
- Non-standard & special custom designed can also be supplied to special order.
2-Poster_HE
Glass Rotary Film Evaporators
Available with CE Marking as per PED - 97/23/EC, The Machine Directive - 98/37/EC, The European Low Voltage Directive - 73/23/EEC, The EMC Directive - 89/336/EEC.
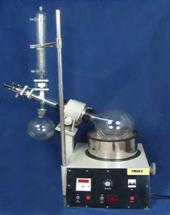 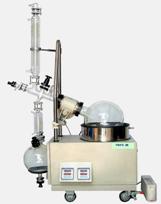
The Rotary Film Evaporator is essentially a Thin Film Evaporator incorporating a rotating evaporation flask. The rotary evaporator will evaporate solvent at a much faster rate than systems using stationary evaporation flasks, due to higher convectional heat transfer coefficient. The rotation transfers a thin film of the liquid to the whole of the inner surface of the flask, markedly increasing evaporation rate due to higher heat transfer between the flask, bath and the thin film. The rotating flask and vapour duct have a sealing system which allows operation under vacuum, further accelerating the evaporation process because of the reduction in boiling point of the solvent and efficient removal of the vapour. Besides the reduction in boiling point there is a considerable decrease in the residence time of the fluid, which also permits heat sensitive materials to be successfully concentrated without degradation. The evaporators can be evacuated down to less than 1 mbar if the vacuum seals are maintained in good condition. A continuous feed facility considerably increases the capacity of the units and distillate withdrawal facilities on some units allow uninterrupted operation.
Features
- Digital display & auto control of rotation speed, vapor temperature and bath temperature.
|
- Miniature circuit breaker and separate power switches for control panel and heating bath offers safety.
- Vacuum Controller (Optional) RS-232 / 485 interface (Optional)
The units can be offered with full automation incorporating a PLC based system or even SCADA for real time data acquisition and control.
There is a range of models covering an evaporation flask capacity from 1 litre 5 litres. The majority of these models may be used on the laboratory bench; the larger models (10, 20, 50, 100 litres and above) are designed for use in pilot plants and production facilities. |
|
Wiped Film Evaporators
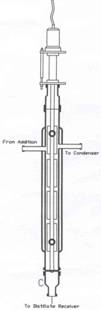 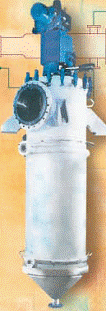 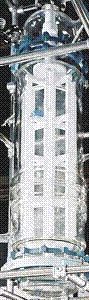
Wiped Film Evaporator is a Thin Film Evaporator and consists of a jacketed glass / SS / other corrosion resistant pipe section in which is rotating a corrosion resistant PTFE / SS / other corrosion resistant wiper system with suitable rows of blades supported by suitable bearings. These give a high wiping frequency and therefore, an optimum renewal speed of the boundary layer, which are pre-requisites for thorough mixing of the liquid film and for high evaporation rates. The wipers are forced against the evaporator wall by centrifugal force, and this can be varied via the speed of rotation of the drive, depending on the viscosity of the liquid.
Inherent features of our Wiping Film Evaporators :
- Made of corrosion resistant materials.
- Lowest possible working temperatures possible.
- Very low residence time.
- Visual observation while using Borosilicate glass.
- Low Hold-up.
- Modular system for all glass components that permits flexible design and rapid assembly of the unit.
- Digital control of motor speed.
- High level of automation (optional)
Mixer-Settler Extraction Unit
The Mixer-settler system is fabricated and assembled in a compact modular design. The mixer as well as the settler are both integrated together instead of being separate entities. This allows the system to be compact and ideal for laboratory and R&D usage. A single stage of Mixer-Settler consists of a mixing zone and settler decanting zone connected to each other through a Weir zone. A brief description of the zones is as follows :
Mixing System
The Laboratory mixer consists of a special glass / ss (as per choice) mixing zone, suitable high speed agitator and a variable speed drive. Besides providing an intimate dispersion the stirrer provides the necessary pumping action. This eliminates the need for external pumps and ensures a large interfacial area for mass transfer. The energy required to produce this dispersion will depend very much on the characteristics of the material and the system used (interfacial tension, viscosity, flow rates, etc).
Between the mixing and separation zones, a weir is incorporated to prevent back mixing taking place and maintains the level of liquid in the mixing zone. Besides it also acts as a baffle to dampen the flow of liquid into the decanter (settler)for enhancing efficient phase separation.
Settling System
The settler comprises a horizontal cylindrical pipe which depending upon size may be one or more pipe sections. From the settler, the outlet of the heavy phase, is controlled by an overflow valve. The design of the settler will be influenced by the throughput of both phases and the material physical properties (density difference, viscosity, interfacial tension etc).
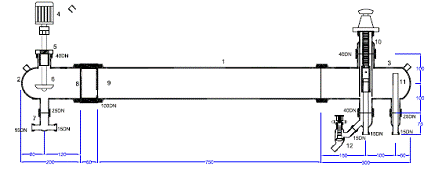
Multi-Staging Mixer-Settlers

Different stages can be connected to each other and the interconnecting pipelines can be done as per your required flow logic. The whole assembly would be controlled through a control panel consisting of suitable circuit breaker MCBs, Relays, digital controllers etc.
Teaching Units / Test Rigs & Miniplants
Teaching units / Test Rigs are possible for various experiments to be performed in chemical engineering laboratories or R&D units pertaining to various processes like distillation, absorption, heat & mass transfer, decantation etc.
Teaching Unit / Test Rig for performance of Falling film and Packed towers with different packings for absorption process.
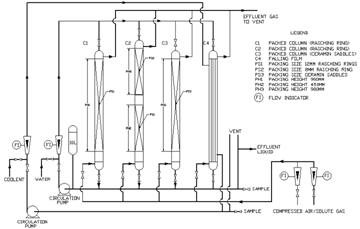
Teaching Unit for studying Distillation / Distillation Test Rig
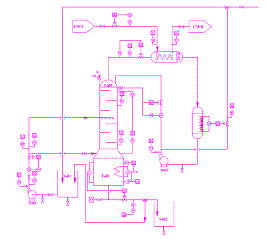
The unit is meant for Methanol-Water distillation. The plant is fitted with an electrically heated reboiler. Vapour generated in the reboiler rises through the column (Bubble cap type / Sieve tray type / Packed column type) and is condensed in a vertical water-cooled condenser.
Plant operation is controlled from a free-standing control panel consisting of flow controllers, temperature and pressure indicators and services controllers.
All major process items and pipework are manufactured from BVR borosilicate glass with other contact parts in , PTFE and stainless steel.
Heat Exchanger Test Rig

The unit is fitted with three heat exchangers namely Shell & Tube type, Shell & Coil Type & Plate Type, each of which can be studied separately. Each heat exchanger can be operated as either a steam condenser or liquid/liquid heat exchanger in counter or co-current flow.
Temperature and pressure indicators are positioned in strategic locations to allow the heat exchangers to be monitored and basic heat transfer mechanisms to bestudied.
The operations can be controlled from a control panel fitted with various controllers. A diagram of the unit is also supplied and this ensures simple identification of valves and recording of plant variables. |